A key design decision I need to make on my way to my DIY trackball is how I would mount/attach the ball. How the ball interacts with the holder through friction and wear etc falls under the study of ‘tribology‘, which originally read like tribolites to me!
There are various arrangements used by commercial trackballs ranging from fixed synthetic ruby balls (Kensington/Elecom), free rolling zirconium oxide balls (Logitech), and roller bearings (CST). Which one is best for me?
Considerations for a commercial product vs a DIY trackball may carry different weights, I have to consider ease of assembly/manufacture so I can make the thing and perhaps not so much on longevity if I can replace or maintain it quite readily.
To make my own qualitative assessments, I 3D-printed test rigs with different arrangements to evaluate the ‘feel’ and ‘noise’ of each.
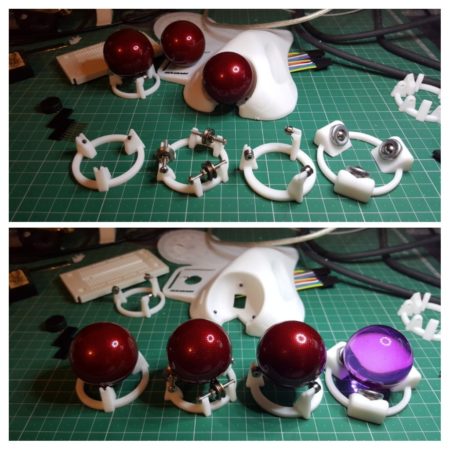
In the picture above are 5 arrangements :-
- Rear (mounted on a test case) – 3 × fixed silicon nitride 3mm diameter balls.
- Left – 3 × loose/free rolling silicon nitride 3mm diameter balls.
- Second from left – 3 × 623VV (3 × 12 × 4mm) V-groove bearings.
- Second from right – 3 × MR63ZZ (3 × 6 × 2.5mm) bearings
- Right – 3 × 8mm ball transfer units.
Qualitative personal opinion wise, the silicon nitride ball setups performed best to my liking in terms of smoothness. I had expected the roller bearings to be the noisiest, but the silicon nitride balls sounded louder but much more tolerable – the metal on metal sound was much more annoying even though it is quieter.
The ball transfer unit set-up did not work well at all, and offered significant resistance. Admittedly these are cheap units, and the grease/oil lubrication that came with them just wouldn’t work as a hand held device.
Between the ‘normal’ roller and the ‘V-groove’ roller which is meant to emulate the design change in CST trackballs, the V-groove performed smoother and more consistently. Not sure if this is the grade of bearings I had, but there seems to be a consensus out there the new rollers on the CST is an improvement, so it is nice to obtain a consistent result with that.
So it is decided, silicon nitride balls it is! With the 3D printing of the test rigs, I designed an arrangement that allowed fitment/replacement of the balls directly in the 3D print without the complication of a custom ‘ball transfer unit’ I had intended to make out of Polycaprolactone (aka Polymorph in Australia).
Next step, electronics, or specifically the laser sensor. Hopefully the PCBs will arrive this week and I’ll have some time the following week to assemble to do some tests with the sensor vs different balls.
STL files for the test rigs here :- https://github.com/madoxnet/trackball/tree/master/hw/test
They are for a 40mm ball. The ball holder is for a 3mm ball bearing; The bearing holders typically are designed to use M3 screws through the bearing hole and either screws through a 2.7mm diameter printed hole or sits on a 3mm diamater channel.
Awesome blogpost, eager to see where this heads you to. For the record, most ergonomic trackball I ever used was the Assassin 3D – there’s a cheap asian clone of it, I even got one but it’s too low DPI so it went to a dark corner 🙂
Yeah this is awesome. Wondering if you could offer some assistance to a noobie? I’m a high level quadriplegic and I’m trying to design a trackball/joystick combination where the trackball will activate micro switches. Reason being is that I don’t have the arm strength to move a standard switch joystick. Please send an email if you have time, thanks in advance.
Hi Glenn,
I’ll love to be of assistance. My own project has stalled due to illnesses but I’m looking forward to kickstarting it again. What do you mean by the trackball activating microswitches? Typically the trackball is only used as the pointing device and separate buttons/switches that act as the ‘buttons’.
What joysticks are you tried? I’m curious what a standard switch joystick is, I’ve seen builds for quadriplegics using ‘arcade joysticks’ which are limit switch based but I find them requiring a fair bit of force too.
Hi Madox,
Thanks for your reply and I’ll see if I can explain my design idea. I currently have a raised desk that I drive my chair under and I control my PC using a mouth operated mouse/joystick, a QuadStick (love this thing). So I had a hole cut in my desk and installed a Zippy joystick (Sanwa copy) and had the shaft cut and machined down to fit a U shaped handle. Problem is it’s still to tall and because I have no feeling in my hands, when I play I can’t tell if my hand is on the joystick or if the joystick has turned/twisted. I also can’t get the handle to grip to my hand so forward and backward movements are extremely difficult. I have tried several joysticks (even an APEM microswitch joystick) and a number of different joystick tops (ball, T & U shaped).
So I had an idea that it would be easier if I was able to rest my hand on the desktop and have a trackball that sits slightly higher than the desktop. So I thought I could combine a trackball top with a joystick bottom, basically have a trackball with a rod screwed in the bottom (rod would be slightly weighted so the trackball/joystick will self centre when left idle) the rod would activate micro switches when the trackball top was moved.
This would make for a joystick that would need next to no force to activate because the ball top would be in/on a holder with minimal friction.
Does this make any sense?
Hello Madox
I’m working on something similar, and very interested in your tests and findings.
Although you last post was in 2017, I’m hoping you are still active.
BR. Lasse Elgaard